HP 3D PRINTER TOUGH ENOUGH TO MAKE BITS FOR YOUR BIKE.
Here at Europac3D there are a few of us who are keen cyclists and last week we thought we would set ourselves a little challenge. We wanted to test how tough is the new PA12 Nylon material from the HP Jet Fusion 3D printer; obviously we could look up the specs on the data sheet, but sometimes ‘the proof of the pudding is in the eating’ as some people might say.
We decided to see if we could replace the existing seat post and seat, including all of the associated assembly components, clamps, rails, bolts etc, and build it all in one piece with a little modification here and there.
Using a Kreon measuring arm and Skyline 3D scanner the team set about scanning the existing seat, post and surrounding area and using Geomagic Design X and the scan data was subsequently converted into a triangulated surface mesh or STL file. This STL was then used as a base object around which new geometry could be designed while still keeping to the specification of the original bike. Design X allowed the team to make the seat stem and surrounding area as aero dynamic as possible and without the use of cumbersome bracketry usually associated with this type of set up. The design phase was finished at the request of the rider to move the seat forward 10mm as he felt he was overreaching a little and that he had reached the end of the adjustment on the current setup.
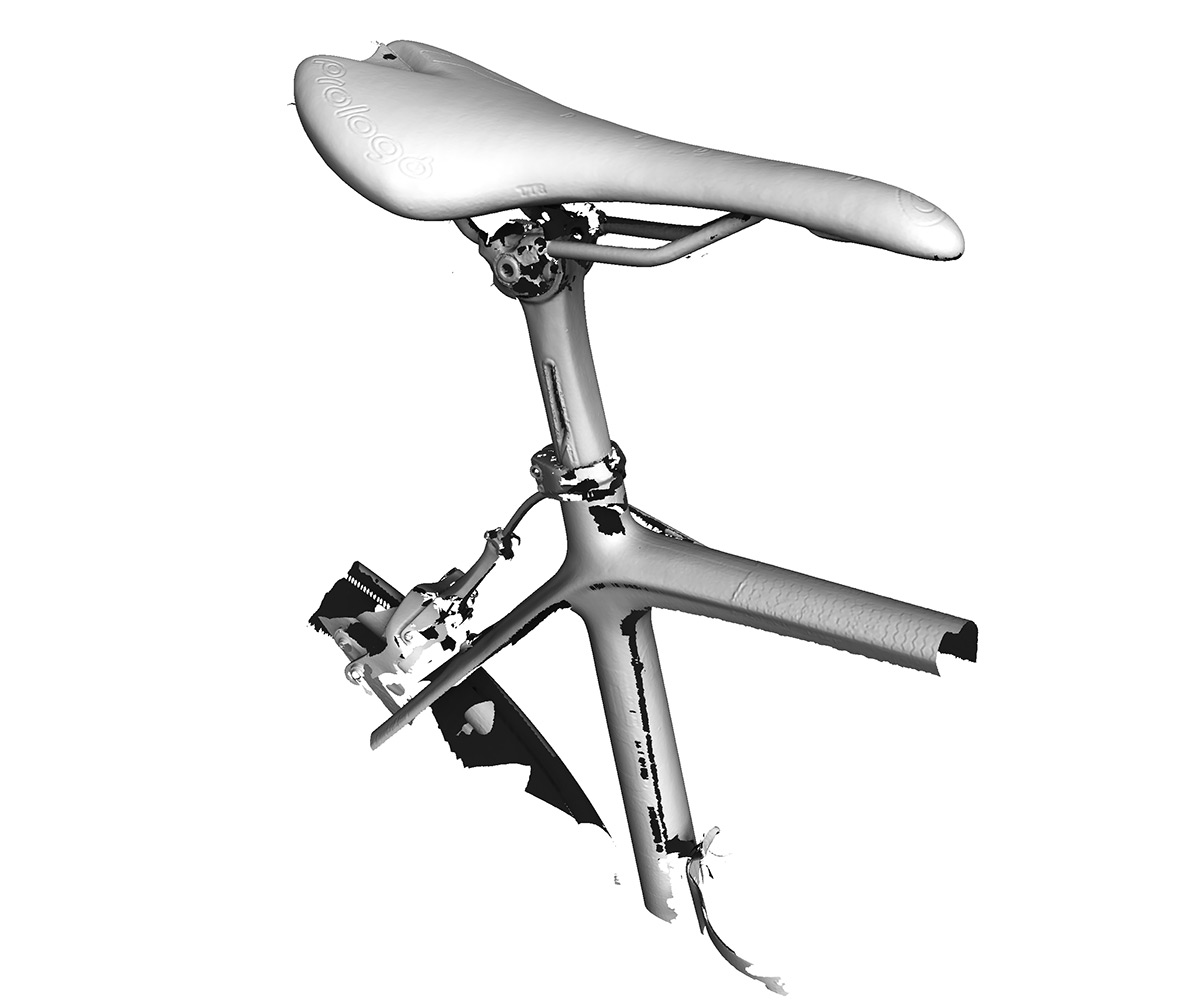
STL mesh of Seat Post and Stem
After the design had be finalised and optimised for aero dynamic efficiency the part was loaded into the HP 4200 Jet Fusion 3D printer. The unique capabilities of this machine are such that the part took just 6 hours to build and a further 4 hours to cool, which is an incredible achievement in comparison to similar SLS technologies. The unique use of HP’s pagewide print head technology means that a single layer can be 3d printed in just 8 seconds, regardless of how many parts are loaded into the build. In fact the machine can be loaded with as many parts as possible and still only take 10 hours to build them. This advance in technology heralds a new era in production 3d printing that will expand the possibilities of 3d printing beyond anything seen previously. The final single piece part weighed just 350 grams compared to 500 grams for the old post and seat, saving our rider a whopping 150 grams.
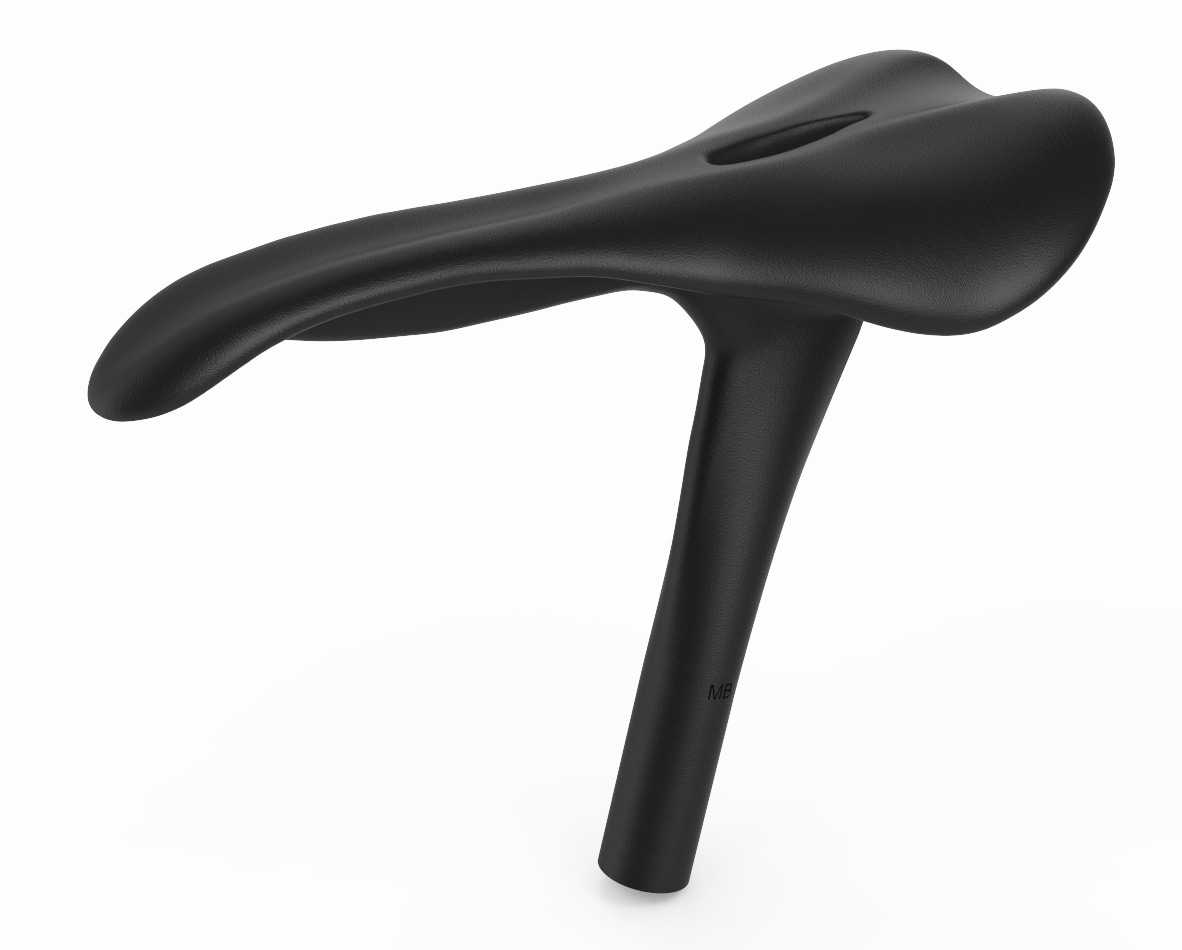
Finished HP Jet Fusion 3d printed seat and post in PA12 material
The new single piece post and seat was fitted to the bike and so far our rider is loving his new seat. He has stated that although the seat is printed in hard plastic there is more flex in the overall setup than he had previously and therefore it is actually more comfortable than the standard seat.
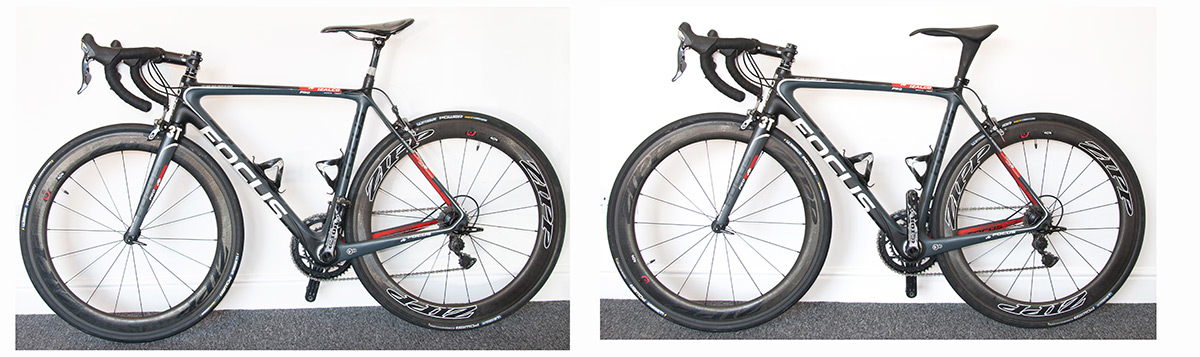
Before and After shot of 3d HP 3d printed seat
We are looking forward to the next stage in the HP development process when more and more materials are made available on this open platform, who knows what we will be able to design and replace next! To see this and many more examples come see us at the TCT show from September 26-28th on stand D50.